Key to Pipe at the Speed of Light
Grace Episcopal Church
Hartford, Connecticut
Schoenstein & Co. and Peterson Electro-Musical Products Inc.
View an enlarged cover
View the Stop List
For generations, Grace Episcopal Church has held a well-deserved reputation for its traditional Anglo-Catholic liturgy and its fine music program headed by Kyle Swann, who is also lecturer in opera at Yale University. The church is quite small, seating only 112—a village church in the heart of a big city. It has a very pleasant, resonant acoustic; amid the grandeur of the ceremony, the setting seems spacious. However, space for the organ is another matter! Sixteen stops, 18 ranks was the absolute limit without encroaching upon already-tight space for choir stalls and pews.
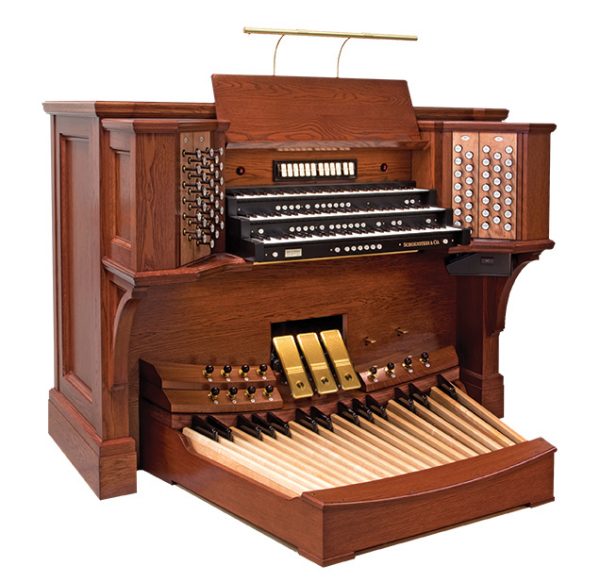
The Anglo-Catholic service places great demands upon the organ. Three qualities are absolutely necessary. First, variety of well-differentiated tone colors. Second, wide dynamic range from ppp to ff. Third, flexibility of control. The first two of these are obvious from the stoplist. There is a complete ensemble of tone colors quite distinctly different from one another just as are the wind instruments of the orchestra. Dynamic range is aided by having Great and Swell separately enclosed and the Tuba Minor with strings in a third expression box located within the Swell. The third key element, control of these resources, is usually just a footnote or completely neglected on the stoplist. All the complex mechanisms that make the modern console aids possible seem mysterious. In this article, we will reveal some of what goes on behind the scenes in the nerve center of an electric pneumatic organ—the electrical control system.
What is the organ’s electrical control system? It consists of two main elements. First, the relay and switching system, which could be compared to a telephone central switchboard taking signals from keys, stops, and couplers and distributing them to the actions that operate the pipes and expression motors in the organ. The second is the combination action that makes it possible to pre-set combinations, to have reversibles and other console playing aids. There are many varieties of systems involving electromagnets and/or pneumatic motors that move contacts much like those in the wall switch turning on and off your lights. On a three-manual organ with 215 keys, 77 stopknobs, and 44 pistons, you can imagine the number of contacts required and the bulk of machinery to operate them.
The advent of solid state has revolutionized this whole process. What is solid state? Very simply it means that all of these electrical transactions are done with no moving parts except the initial contact at each key, stop, and piston. This results in a vast miniaturization of the systems. It also eliminates the need for air power and replacement of contacts and leather.
Here is what the electrical control system does for our Hartford instrument. Of primary importance is unification, sometimes called duplexing, or extension. This allows a stop to be played at different pitches on one manual, to be borrowed from one manual to another or extended into the Pedal. If done with care, this can easily double the effectiveness of an instrument. This installation illustrates one of the most valuable uses of unification—creation of a third manual so helpful especially in service playing. Solo stops from both manuals, accompaniment stops from both manuals and a small “Positiv” ensemble from the Swell are immediately available.
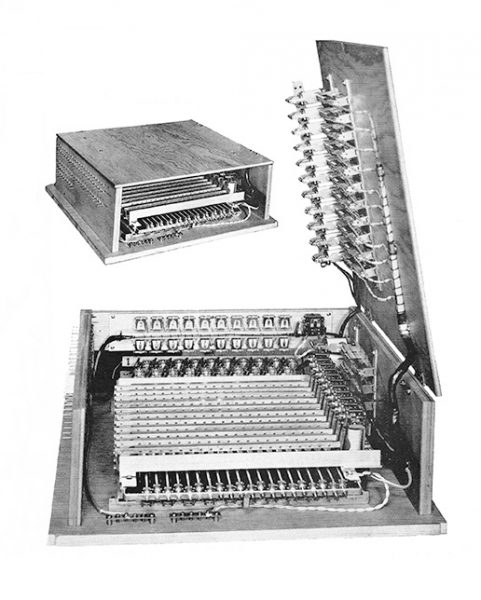
The console has an extensive combination action with a generous number of pistons and 100 assignable and lockable memory levels. The stops affected by a piston can be programmed via a feature called “compassing” whereby, for example, divisionals can become generals. There is a piston sequencer to allow moving through the sequence of general pistons by simply touching the Advance piston. It has a record/playback system and numerous other features including the ability to memorize combination settings and store them on a memory stick.
Most of these control features would not be possible at Grace Church without the most recent revolution in solid-state technology, the integrated control system; in this case, a Peterson model ICS-4000. There wouldn’t be enough space to house the necessary electropneumatic equipment and a good many of the features including multiple memories, piston sequencer, and record/playback would not be practical even with unlimited space.
The evolution of modern control systems started in the late 1960s, when early versions of solid-state switching systems appeared on the market and began to be incorporated into the instruments of some forward-thinking and adventurous pipe organ builders. Those early “diode matrix” switching systems offered, for the first time, a more cost-effective and far more compact way to connect an organ’s key and stop control contacts to its note actions using no moving parts, no perishable materials, and far fewer electrical contacts to periodically clean and maintain. Soon, separate solid-state electronic combination actions such as Peterson’s original “DuoSet” single-memory model were developed utilizing digital integrated circuit memory. Interestingly, many of the very first pioneering pipe organ installations are still in service today and diode matrix switching systems continue to be built for some new organs and rebuild projects. But over the years, steady advances in available technology have been utilized by control system suppliers to offer far greater capacities, a long list of creative features, ever-smaller size, and much lower relative cost.
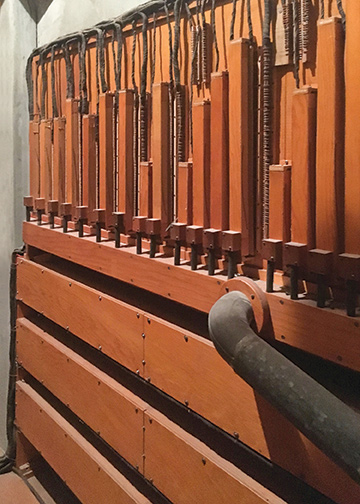
One of the critical strategies has been to “integrate” organ control subsystems—relay and switching, combination action, transposer, manual transfer, reversibles, vast amounts of piston memory, programmable crescendo and tutti, piston sequencer, MIDI interface, and record/playback—into a single all-encompassing microprocessor-controlled system . . . thus the term “integrated control system.”
While some of these features of integrated control systems may be deemed unnecessary and even inappropriate for particular pipe organs and may be left out, the principle behind the efficient implementation of such a system is generally the same. Microprocessors and microcontrollers can be thought of as tiny but very powerful computers that accept inputs, process those inputs based on software instructions, and then drive outputs to accomplish the required tasks.
A pipe organ control system’s inputs consist of electrical voltages that appear at system inputs when keys, stop and coupler controls, pistons, expression shoes, and other miscellaneous console controls are operated. Through an extremely fast, constant, and repetitive scanning process, all of an organ’s inputs are sampled quickly enough that any change, such as the press or release of a key, will be processed so quickly that no delay is discernable to even the most proficient organist playing as rapidly as possible.
The efficiency of an integrated control system’s size, cost, and performance is accomplished largely because, once inputs have been scanned, the resulting data can be manipulated by the microprocessor and microcontrollers with remarkable speed and precision, and surprisingly few parts, given careful software design. Whether used to run a small pipe organ like the instrument at Grace Episcopal Church in Hartford, or an enormous recital instrument with two consoles and every imaginable convenience for organists, integrated control systems have truly revolutionized the way electric-action organs are controlled today.
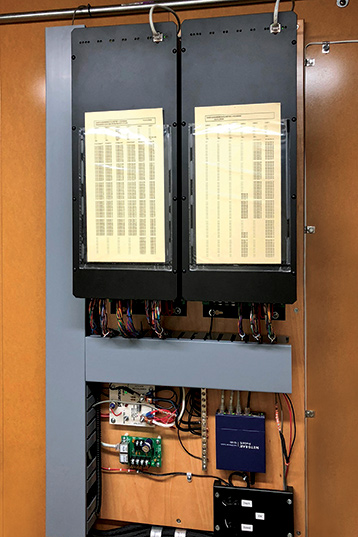
The Grace Episcopal Church organ was completed on June 26, 2017, and was featured in a dedicatory recital by Thomas Murray on October 29, 2017. The priest-in-charge is the Rev. Rowena J. Kemp and the director of operations in charge of preparing the installation site was parishioner Tom Phillips. This was a project we enjoyed thoroughly, especially due to the strong cooperation, encouragement, and enthusiasm of the entire parish.
Jack Bethards, President
Schoenstein & Co.
Scott Peterson, President
Peterson Electro-Musical Products Inc.
Cover feature photography: Louis Patterson