Trinity Cathedral
Cleveland, Ohio
Muller Pipe Organ Company
Croton, Ohio
Stoplist
From the Director of Music
Trinity Cathedral was designed by noted Cleveland architect Charles F. Schweinfurth (1856–1919) and is one of Cleveland’s most tastefully lavish church buildings. It was consecrated in September 1907, and one month later Ernest M. Skinner’s Opus 140 was dedicated by Edwin Arthur Kraft, who presided over it for the next 52 years. Initial plans for Opus 140 were drawn up during the brief and tumultuous partnership between Skinner and Robert Hope-Jones, although Hope-Jones departed prior to the installation. Kraft and Skinner revised the specification somewhat, though the resulting organ retained Hope-Jones’s influence in two of its most notable features: the double-pressure 32′ Diapason and the high-pressure Tuba that spoke from a concrete-lined chamber in the floor at the rear of the nave. In 1956, Schantz Organ Company rebuilt the instrument under Kraft’s direction, as he wanted to leave Opus 140 in good condition for his successor.
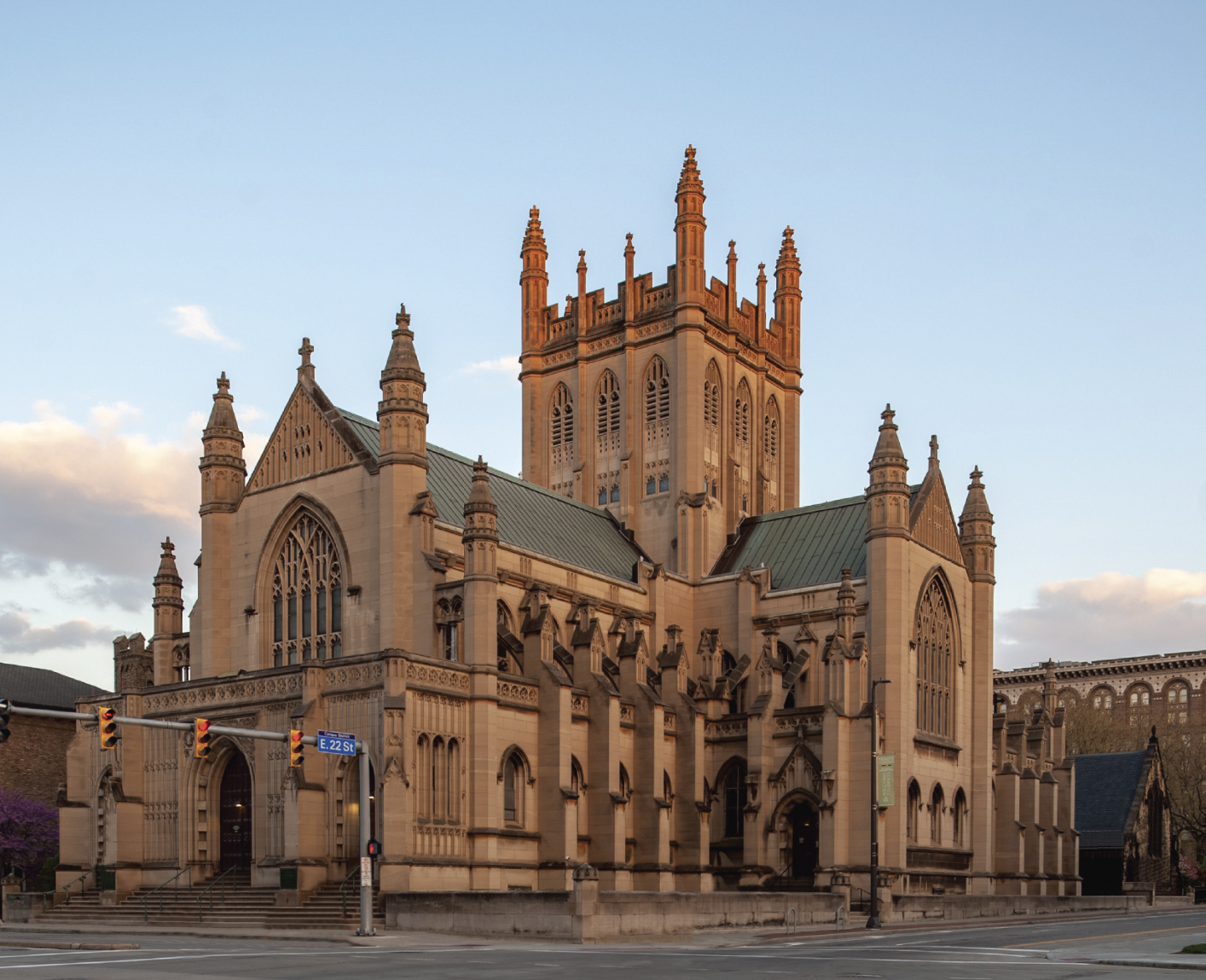
Winds of change were blowing in the American organ world, and by the late 1960s conversations were underway for a new cathedral organ. In 1977, D.A. Flentrop installed a handsome three-manual, 39-stop instrument with mechanical key and stop action in a new gallery on the liturgical west wall. The Skinner was abandoned and became unplayable, with its chancel tone openings sealed up. In 1997, the Skinner was removed and its pipework dispersed to several builders. The former Skinner chamber became a spacious and characterful choir rehearsal room.
I came to Trinity as organist in 2009 and became music director two years later when my predecessor, Horst Buchholz, moved to St. Louis. I felt strongly that Trinity Cathedral, with its divided chancel and elegantly carved choir stalls, should have an organ at that end of the building. We have the good fortune to sing Evensong on a weekly basis during the academic year; yet the Flentrop, while a beautiful and remarkably versatile instrument, is not an idiomatic or convincing organ for accompanying Anglican repertoire. The lack of any combination action can make accompanying a physical and musical challenge.
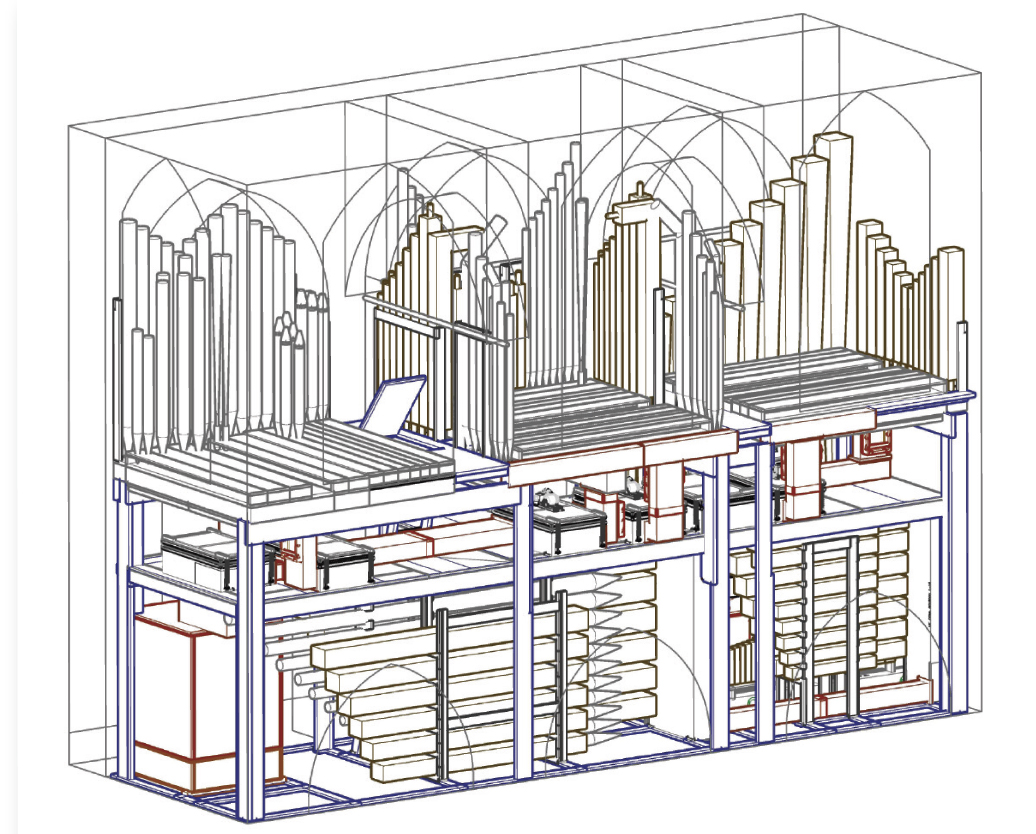
In a leap of faith, we purchased Aeolian-Skinner Opus 1188 in 2011 from St. Anne’s Episcopal Church in Reston, Virginia, where it had been moved from its original home at St. Paul’s Episcopal Church in Richmond. The organ was put in storage at the Muller Pipe Organ Company near Columbus, Ohio. In 2014, our bishop, the Right Reverend Mark Hollingsworth, allowed us to remove the remaining pipework from Skinner Opus 245 from the cold, unfinished undercroft of Cleveland’s Church of the Transfiguration just days before its demolition. These additional ranks joined the Aeolian-Skinner in storage at the Muller facility.
Over the next few years contributions from three leading donors paved the way toward making the new organ a reality. The remaining funds were given by Trinity parishioners, choir members, and friends, along with a generous grant from the Wyncote Foundation and the sale of Trinity’s small two-manual chancel Flentrop.
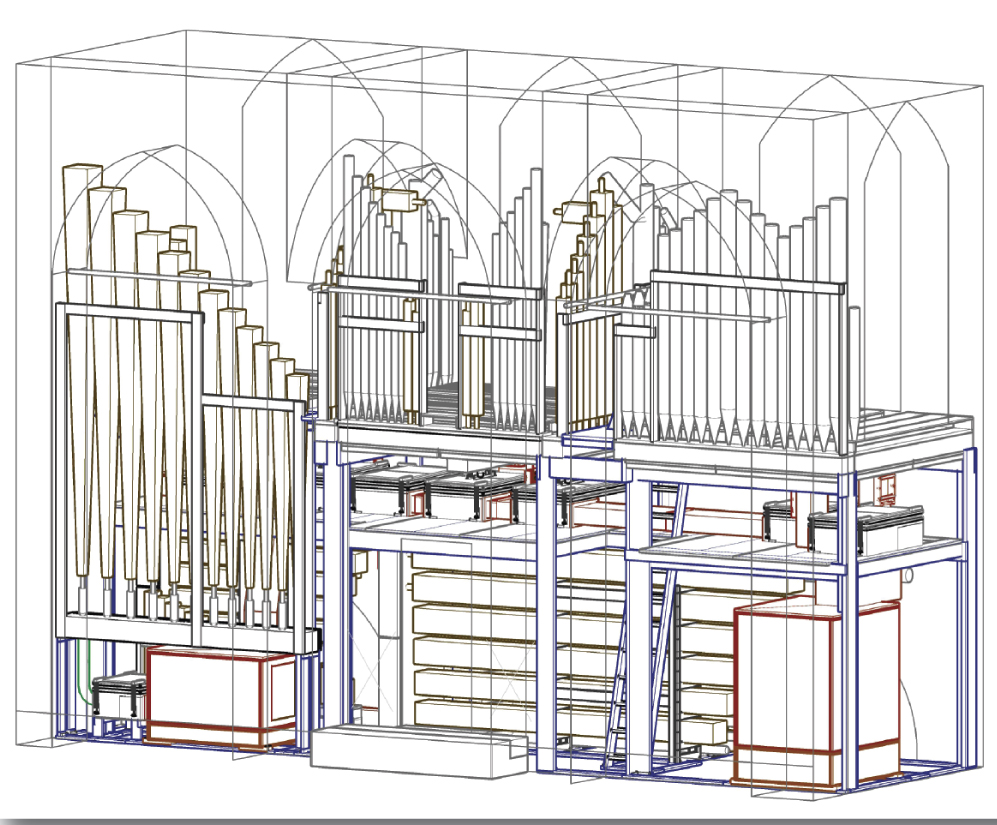
I have known the Muller Pipe Organ Company for most of my life, as a previous generation of Mullers were the primary organ maintenance men in my hometown of Toledo, Ohio, and were endlessly kind and patient with a curious boy who was full of questions. In 2006–7 I saw the present Muller Company (two active generations) work miracles in reconstructing Skinner Opus 647 at Lake Erie College in Painesville (just east of Cleveland) and was confident that they would be able to provide similar results at Trinity Cathedral.
That they have done. The chancel organ in Trinity Cathedral is essentially a new instrument, combining pipework from Opus 245 and Opus 1188 with ranks of new vintage-style pipework as needed. The instrument takes up one-third of the previous organ chamber, speaking through the now reopened arches into the chancel and east transept. The Choir division occupies the smaller chamber to the right of the chancel, where the original Skinner Choir was located.
The chancel organ, together with our wonderful Flentrop (an instrument that has taught me so much), will open an exciting new chapter in the liturgical life and musical outreach of Trinity Cathedral. The two organs provide contrasting tonal palettes, each valid, beautiful, and convincing in its own right. The Cathedral Choir will once again be able to sing accompanied music from the chancel as architect Schweinfurth intended. An organ with pistons, swell boxes, and celestes, and with an enormous dynamic range and a wide variety of beautiful solo stops crowned by a heroic Tuba, will truly be a “new day” for us at Trinity Cathedral.
My gratitude goes to the staff of Trinity Cathedral, the Rt. Rev. Mark Hollingsworth, the Very Rev. Tracey Lind, the Rev. Dr. Paul Gaston, and our current dean, the Very Rev. Bernard J. Owens. Without their support this project would not have come to fruition. Soli Deo gloria!
Todd Wilson
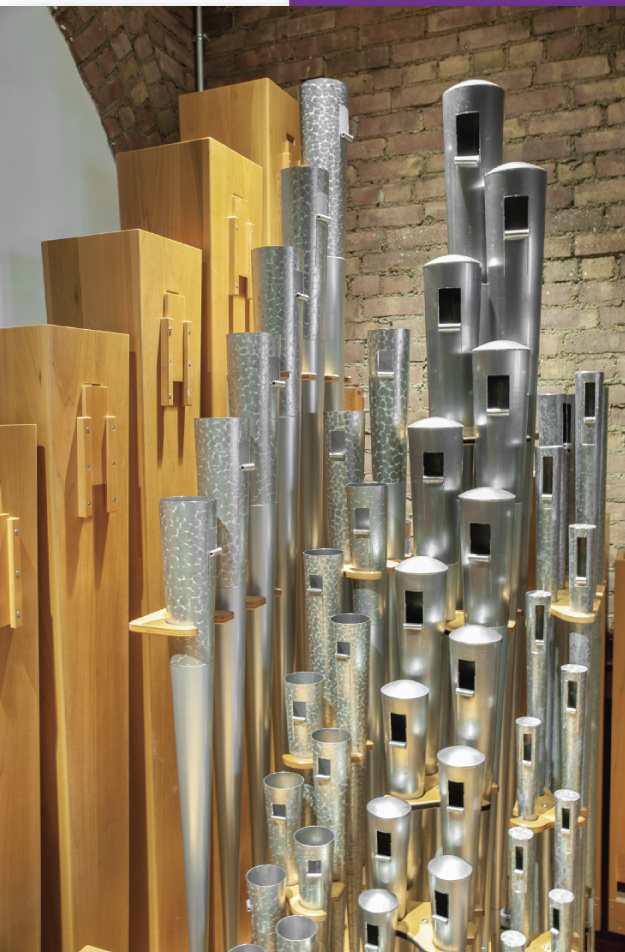
From the Builder
When approached by Mr. Wilson about installing an instrument in Trinity Episcopal Cathedral, so much was immediately imaginable. We knew the legacy of the Skinner organ designed by Edwin Arthur Kraft, and the continuing distinguished voice of the Flentrop. What kind of instrument would be suitable?
The project started simply: move and restore the mostly extant Aeolian-Skinner Opus 1188, itself a redesign of an earlier Lyon & Healy organ. However, in a cathedral known for its fine instruments and exquisite music, installing a modest 40-rank organ seemed rather lackluster. Was there a way to provide a pipe organ in proportion with the grandeur of its future home?
The answer presented itself a few years later when pipework became available from Skinner Opus 245, another organ on which Kraft consulted. These pipes provided the catalyst for the instrument’s unique tonal concept.
The resulting instrument does not fit cleanly into any traditional category of organbuilding. It is not a rebuilt organ, nor is it a restoration or renovation. Neither can it be described as an Aeolian-Skinner or Skinner organ. Rather, we have developed elements of its historic lineage to form a new instrument with a broad spectrum of foundation tone, colorful reeds, a variety of flutes, and sublime strings. Creatively reimagined using vintage and new pipework, this “heritage” instrument is the type of pipe organ that Muller has produced with great success in a variety of projects.
All stops were carefully auditioned then seamlessly incorporated into the new tonal scheme through an extensive voicing process. The Great division retains the tonal design of Opus 1188 with a few additions. The large Diapasons are from Opus 245, but the bulk of the pipework for this division is new. The Swell and Choir division pipes are largely from Opus 1188. The Choir organ incorporates a Dulciana and Unda Maris from Opus 245 and a repurposed Principal from Opus 1188.
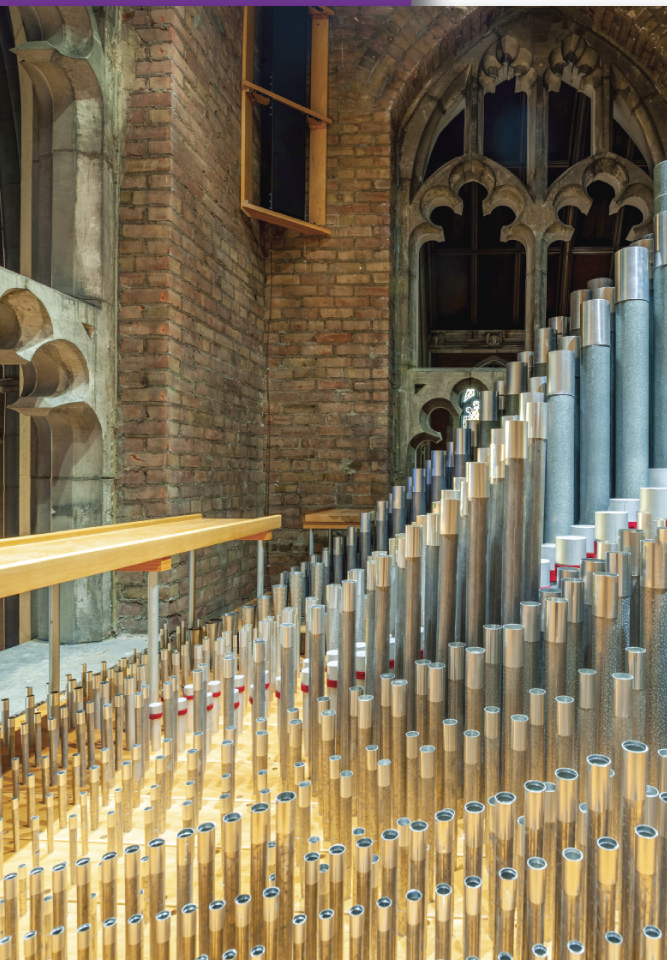
The Solo organ utilizes new pipes, plus pipes from Opus 245 and other vintage sources. Of note is the Dulcet II, a particularly keen and small-scaled set of strings. This rare stop was rescued from Opus 245 and restores a part of the original Skinner tonality to the cathedral. And while Opus 245’s Tuba was damaged beyond repair, a new Tuba was fashioned following its pattern by A.R. Schopp’s Sons. The resulting stop, of epic proportions, is a worthy replacement for the original Skinner’s subterranean Tuba. Like many early 20th-century instruments , the Pedal division is only two ranks and uses extensive borrowing to ably undergird any possible manual combination.
The return of an organ to the cavernous chambers of the original Skinner posed significant challenges. The new, larger instrument now occupies a fraction of the original space and is situated in shallow chambers to maximize tonal egress. The larger pipes of the Pedal division rest horizontally on the first level. The second level functions as a mechanical mezzanine for reservoirs and provides easy access to the manual windchests for maintenance. The uppermost level, with stone tracery aligned with the east clerestory windows, is home to the manual windchests. The Choir division returns to its original Skinner chamber.
The Aeolian-Skinner console from Opus 1188 was retained. The cabinet was repaired and refinished to complement the furnishings of the cathedral. Improvements include a new solid-state control system with remote tuning capability, Skinner-style bench with adjustable mechanism, replica interior components, and bone manual keys. Windchests from Opus 1188 were restored for the bulk of the Swell and Choir organs, while new ones were provided for the remainder of the instrument.
We wish to extend special thanks to David R. Beck for sharing his string voicing expertise, to our supplier partners, and to Todd Wilson, Nicole Keller, and the staff at Trinity Cathedral. It has been an honor to be a part of this monumental project to return a thrilling element to the cathedral’s pipe organ tradition. Trinity is located in the heart of a truly American city, and it is fitting that this Episcopal cathedral can again celebrate its musical heritage with a truly American instrument.
Scott G. Hayes, Tonal Director
Jack Muller, Project Manager
MullerPipeOrgan.com
Muller Pipe Organ Company
Brad Ashbrook
Nathan Baker
Ryan Boyle
Jesse Braswell
Scott Hayes
Taylor Hendershott
Mike Hric
Jack Muller
Jane Muller
John Muller
Mark Muller
Stan Osborn
Photography: Jesse Braswell