St. Dunstan’s Episcopal Church
Shoreline, Washington
Ortloff Organ Company
Needham, Massachusetts
Stop List
By Jonathan Ortloff
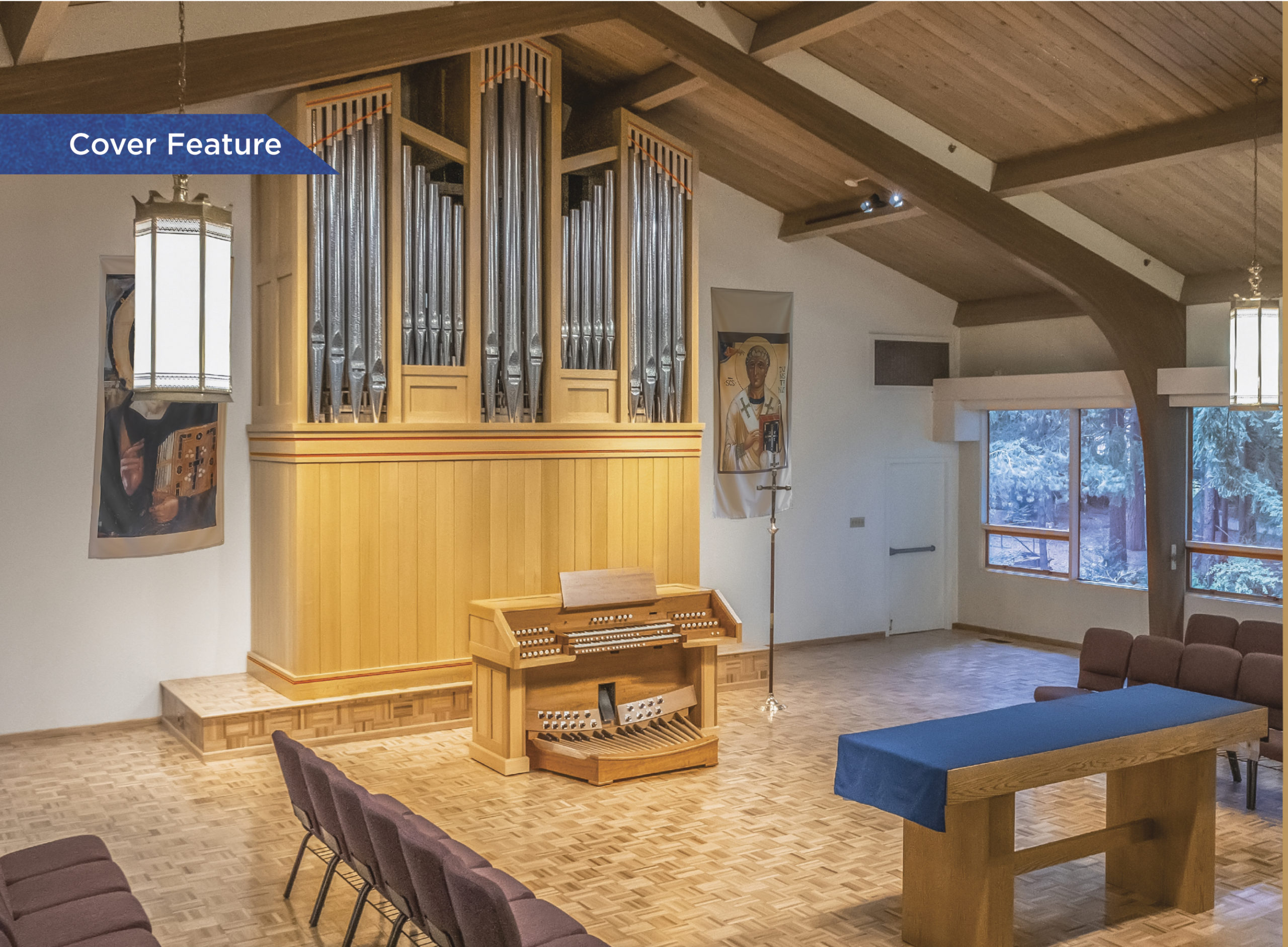
To get a sense of the conviction with which St. Dunstan’s Episcopal Church performs its ministry, visit the church any Tuesday. On those evenings, for the last eleven years, whether rain, snow, or global pandemic, dozens of church members have prepared a huge meal and fed it to more than 250. No wonder that throughout greater Seattle, St. Dunstan’s is known as “the church that feeds people.” The scale of such ministry belies the fact that St. Dunstan’s, like many Episcopal parishes, is a suburban church of modest size. Yet that size has never prevented the parish from entertaining larger visions, either pastoral or musical.
The dedication to outward-facing ministry exemplified in St. Dunstan’s feeding program is matched by a robust commitment to ministry within the congregation. Led by the energetic rector Rev. David Marshall, the congregation is full of hearty, devoted members who throw themselves into the various ministries of the parish with great conviction. This is a church that values music as a ministry, with a spirited program under the direction of Susanna Valleau, encompassing a growing adult volunteer choir and a large lay-led handbell ensemble.
Sixty years ago, St. Dunstan’s had grand plans for a complete campus on a wooded retreat. A familiar reality set in, however, as money wasn’t readily come by, and in the end the congregation raised enough to build a parish hall; the church proper would remain a blueprinted intention. In turn, the hall became a de facto worship space, with a secondhand Hutchings-Votey installed by “the men of the church.” Nevertheless, the people of St. Dunstan’s never stopped dreaming of a new organ, starting a fund for one 22 years ago.
Our company’s relationship with St. Dunstan’s began in the winter of 2018, when I was asked to consult about the logistics of installing a particular vintage organ there. As I would learn, the organ committee was a tight-knit, devoted, and fun group; having done thorough homework, they asked smart questions. Their commitment to making the best decision was born out of a shared dedication to ministry and character. They wanted an instrument as unpretentious as the congregation and the space, one well suited to the distinct worship there. But they wanted something more than mere variety from a limited number of stops: they wanted an organ of character. Moreover, they had already deduced that greater Seattle was rich in mechanical-action organs, of many sizes and tuning systems. A small electric-action instrument in equal temperament, with something of a Romantic bent, was for St. Dunstan’s a way to provide variety and be part of a larger mission of musical stewardship in the community.
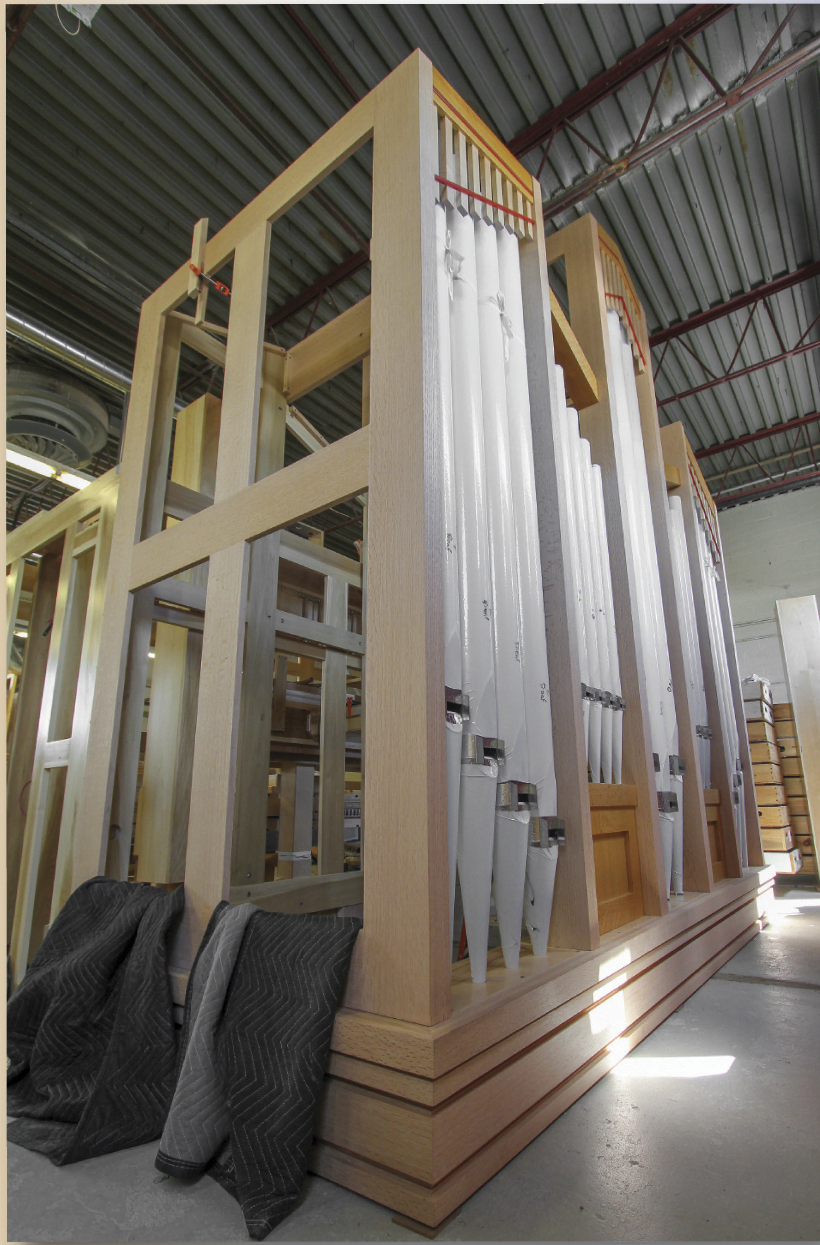
When it became clear that the complex space effectively demanded a custom-designed new organ, the committee decided to commission one. Because of the relationship established during that initial phase of inquiry, they went to see our Opus 1 in Penfield, New York. In turn, and quite flatteringly, they decided to commission our Opus 2.
On the mundane face of it, organ projects are about designing cases and mechanisms; building pipes, structure, chests, and action; and voicing and tonal finishing. What happens in the workshop, however, is almost always a reflection of something deeper: the relationships formed in shaping and completing the project itself. And in this instance, those bonds were early and strong, making the experience all the more fulfilling. With shared interests in boatbuilding, woodworking, rowing, and our common faith, Rev. Marshall and I were fast chums. Out of that relationship came trust, no small matter for just the second instrument from an organ shop, one being built on the other side of the continent and 16 months in the future. When it became clear that our shop’s COVID shutdown at the pandemic’s height would delay the organ’s completion, Rev. Marshall said frankly, “Having an organ for Pentecost [the original goal] seems so unimportant now. You take care of your people; we’ll take care of ours, and we’ll all be elated whenever this instrument sounds in our church for the first time.” Chris Johns, St. Dunstan’s clerk of the works and a retired Boeing engineer, guided the project from the church’s end and dedicated himself to designing and completing the infrastructure to support the new organ “the right way.” Ever cheerful, he always made himself available to check measurements or to consult on technical matters, returning data on beautiful, hand-wrought scale drawings.
Perhaps most important in the building of a musical instrument is a strong relationship such as the one that grew with St. Dunstan’s organist and music director Susanna Valleau. A graduate of Lawrence University and the University of Washington, she has served the parish for six years. Susanna and I met while working at the 2011 AGO Pipe Organ Encounter in Boston, and we renewed our connection on this project. Her enthusiasm throughout the job injected energy into both the parish and us as builders. She visited twice during construction, and her excitement in seeing and hearing parts of the new instrument encouraged us in our work. Most importantly, she and I had broad agreement over a vision for the organ: one that put accompaniment of the Episcopal liturgy right out front.

Our proposal stated the organ’s chief goal as providing “not just support for congregational and choral singing, but an ensemble that energizes and compels worshippers to sing, and serves as a partner in that singing.” In a room that seats 200, we were sensitive to providing an ensemble that would energize without being overbearing. To this end, the overall tonal goal was to voice chorus work with both warmth and a scintillating yet restrained energy, something that gives the impression of grandeur without being plainly loud. In my view, this kind of voicing, aided by high-lead alloy for much of the pipework, truly does compel singing.
My experience as an Episcopal church organist informed much of how the organ’s stops are arranged, scaled, and voiced. Chief among those choices was placing both reeds and the organ’s sole mixture in the Swell. Two factors are at play here. In this intimate, nonreverberant space, intense upperwork to complete the Great chorus was desirable, but it ultimately benefited from the moderation provided by enclosure. Just as important, intense mixture tone, merged with reeds, all closed down behind shutters, is one of the most thrilling and necessary sounds for accompanying. In this instance, the mixture clearly belonged in the Swell. Thick shutters ensure proper caging of the lion.
Nestled among the basics are certain effects that suggest big-organ grandeur: bold strings, a soloistic Harmonic Flute, a rich, warm 16-foot chorus. At the same time, delicate, intimate voices that might otherwise get lost in a larger room were included here to good effect, such as the Swell’s quirky Spindle Flute. The resourceful organist will find many opportunities for color here, particularly using stops up and down octaves.
Beyond the new relationships a job fosters, existing relationships with longtime colleagues bring the talents and skills to complement those of our shop. As in past jobs, I turned to my mentor Steve Russell for the construction of many pipes. Our relationship goes back to my very first day as an organbuilder, spawning nine years working in his shop. Having that deep common experience means that we speak exactly the same language when it comes to pipe construction. The strings, facade, and reeds were made by Shires Organ Pipes of Leeds, England—a new relationship for us. Terry Shires asked all the right questions of a new customer and was attentive to our requests in the smallest detail. Reed voicer Chris Broome and I burned up the ether texting back and forth about every little thing having to do with a mere two reed stops. His concern for their success, from the initial samples through to tonal finishing, mirrored my own. Christoph Wahl provided vital assistance in the construction of slider chest grids, and finally, Organ Supply Industries expertly made wood pipes to our specifications.
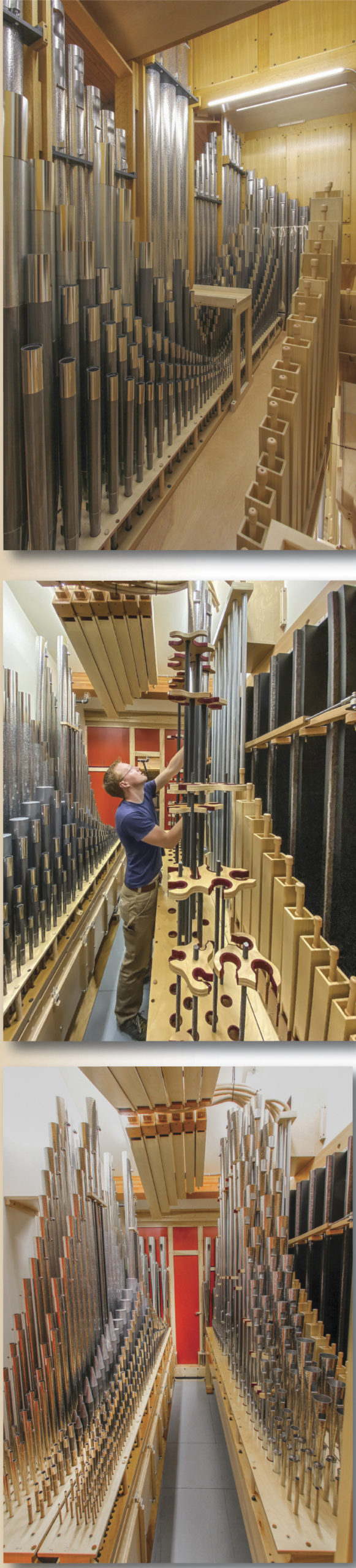
The completion and installation of this instrument was, like everything else in 2020, beset by the COVID-19 pandemic. Our shop shutdown for three months meant that meeting the original installation schedule was impossible; moreover, our concern for safe travel put a question mark over the end of the job. Would we fly? Would we stay in a hotel? Where would we eat? How long could we keep this completed instrument in our shop waiting for the pandemic to recede? With seemingly no end in sight, we convinced ourselves of the safety of flying, elected to stay in an Airbnb, and set a late August date for installation. As in past jobs, we turned to our long-standing relationship with the Organ Clearing House crew—Amory Atkins, Terence Atkin, Josh Wood—to ensure a successful installation. Once on site, I was not a little proud to see an instrument that had taken 16 months to build get erected and fully piped in merely four days. Finally, Duane Prill joined me for two weeks of tonal finishing.
The joy of this organ’s completion was twofold for our company: not only in building the instrument, but in seeing the impact it has had on the people we developed close relationships with over the past three years. These warm relationships feed us as we journey through a project with a church, and we are blessed to have truly made new friends at St. Dunstan’s. For these good people, Ortloff Organ Company is honored to offer this, our second opus, to this hearty parish. It is my hope that it will feed the church that feeds people for generations to come.
Ortloff Organ Company
Bart Dahlstrom
Corey DeTar
Jonathan Ortloff
Patrick Walsh
Jonathan Ortloff is the founder and president of Ortloff Organ Company, LLC. He holds degrees from the Eastman School of Music and the University of Rochester in organ performance and engineering.
I can only say how flattered I am to have been mentioned in this article. Jonathan Ortloff and his team are professionals. During the building of Opus 2, Jonathan Ortloff was personable, accessible and always the professional. Of course there were moments of levity, especially when he and team members joined us for an occasional dinner.
Opus 2 was built with care, perfectionism and, clearly, great expertise.
It was a pleasure to deal with the Ortloff Organ Company who delivered St. Dunstan’s Episcopal Church a fine musical instrument as promised for the agreed upon price.
You are true craftsmen, musician, fine people and good guys! Thanks to the work of Ortloff Organ Company our expression of ministry in music is a living work in progress. Worship of the Holy One raises the hearts of all who come. I stand in awe and respect of your great talent.
Opus 2 is indeed a remarkable instrument. Thanks to all the members of Jonathan Ortloff’s amazing team!