Northrop Auditorium and its Reconditioned Aeolian-Skinner
Opus 892
by Mike Foley
View an enlarged cover
View the Stop List
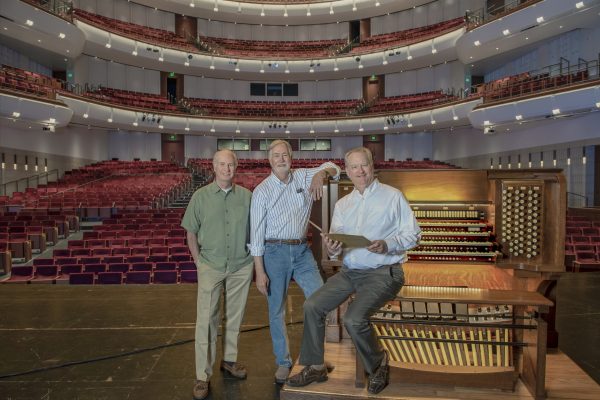
Completed in 1929, Cyrus Northrop Memorial Auditorium was named after the University of Minnesota’s second president and remains an iconic structure on the university’s Minneapolis campus. The Aeolian-Skinner, Opus 892, was installed in four sections between 1932 and 1935. We were called to survey the organ in 2009. Northrop seated 4,847; it was a distance of 206 feet from the stage to the balcony’s rear seats. From there, one almost needed binoculars to see the console. I was used to seeing a theater’s organ chambers in the side walls aiming the sound squarely at the audience. Here, the pipes were in chambers placed above the proscenium arch and nearly buried against the rear fly-walls. A sculptured plaster tone chute struggled to direct sound down and through a ceiling grille. The organ’s doom was nearly sealed when a huge acoustic shell, an attempt to improve the sound of the Minneapolis Symphony Orchestra, was constructed in the late 1960s. It extended out about 30 feet from the top of the proscenium, leaving the organist, in the orchestra pit far below, so separated from the sound that one could think it were coming from another room.
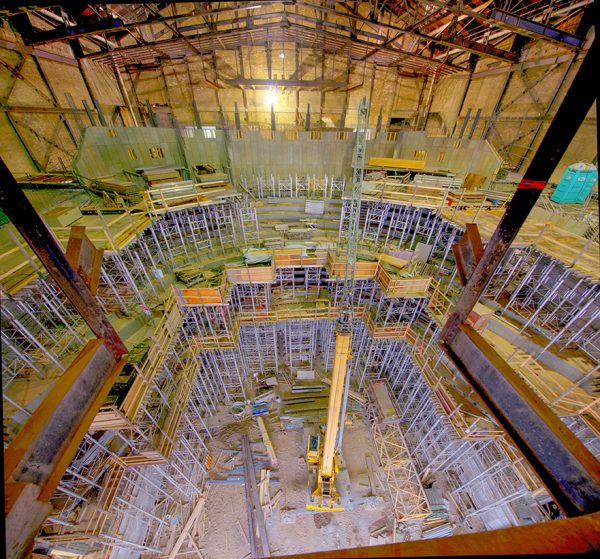
The console enjoyed a separate lift in the center of the otherwise stationary orchestra pit. More than marred, its cabinetry had been damaged over the organ’s first 50 years. The vertical selector combination action was on its last legs. Lack of light made it feel as if you were nearly playing in a cave.
On the other hand, partly thanks to the fact they were difficult to access, we found the chambers essentially untouched. Had time stopped? University organist Dean Billmeyer and those that preceded him genuinely appreciated Opus 892 and had closely watched over the instrument. After 76 years, chamber equipment was very dirty but not damaged.
The organ was still being used; however, the halcyon days of weekly radio broadcasts and regular use with the Minneapolis Symphony (which, as the renamed Minnesota Orchestra, moved to Minneapolis’s new Orchestra Hall in 1974) were long over. At the time of our survey its use was reduced to convocation and commencement ceremonies, as well as occasional organ lessons and concerts . . . all kept alive by Dean’s good efforts. It was a dirty, old, but fabulous instrument! Needless to say, we were more than delighted to be presented with the challenge of making it look and sound beautiful and work perfectly once again.
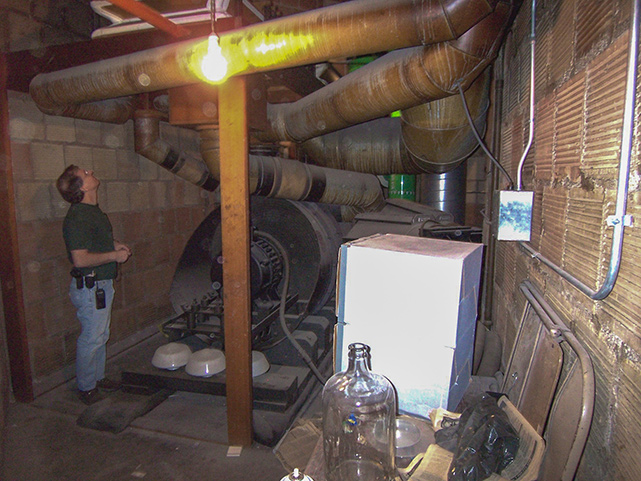
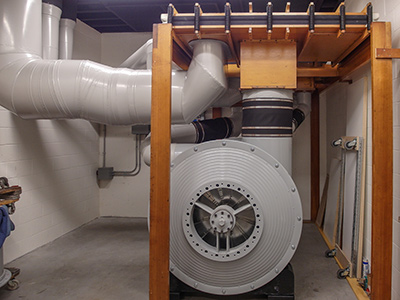
Although Dean Billmeyer had been diligently raising funds to recondition the organ, it was the $88 million building remodeling project that finally launched things. The total interior of Northrop would be gutted to the outside walls. Seating would drop to 2,700 in what would become a stunning, triple balcony, state-of-the-art performance space . . . but beyond chamber preparation, there was no funding for the organ. The good interest of past university president Robert Bruininks, who viewed Opus 892 as a “priceless treasure,” helped secure a generous donation from the estate of alumnus Dr. Roger Anderson. This assured that the Aeolian-Skinner would be totally reconditioned and installed in the new theater.
But where? Along with the rest of the building’s interior, the original chambers would be demolished. The very large 25-horsepower, triple-bearing Spencer blower would need a new isolated location. With the dedicated console elevator gone, space needed to be found for the console’s safe storage. Adequate space for chambers was a big issue, made more complex by the fact that the lineup of uses for Northrop in the 21st century saw the organ rather near the bottom of the list. Regardless, the organ was to be accommodated and the architects were determined to fit it in. Initial concept meetings brought consideration for chambers at stage rear or in the side walls of the new theater. To organists, either would have been most welcome; however, in the end, it was decided that the chambers had to go back above the proscenium arch, which, by the way, was the only original portion of the auditorium that was retained. Even so, the reinstated and compromised chamber placement would come with improvements:
- Rather than speaking into a poorly placed ornamental grille, the complete chambers would instead face directly into a new, 100% diaphanous mesh screen that almost invisibly makes up the massive organ egress surfaces now above the proscenium. Finally, all the organ’s sound would get out.
- There would be nothing, such as the old sounding board, blocking tonal egress.
- A specially designed (sculptured) ceiling would span the entire area in front of the organ chambers and deflect the organ’s sound down toward the stage and into the auditorium.
Indeed, tonal egress is far improved and the sound-deflecting panel works well. The new, deeper orchestra pit makes it possible to place the console further yet toward the audience and almost directly under the chamber grilles above. There’s further improvement when the stage wall-surrounds for orchestra performances are erected.
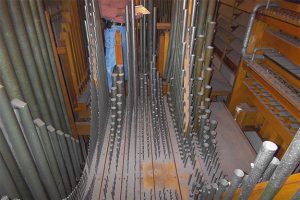
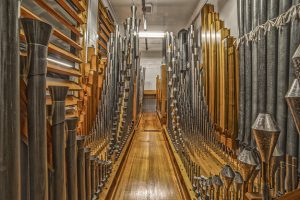
The organ reconditioning process included everything. Virtually every piece of leather in the instrument was replaced. This included every valve and even the valve stems. So that the organist could enjoy the best possible articulation, the double primaries of each action were adjusted to within fractions of an inch. We also used double-tanned pouch leathers that are essentially nonporous. Everything was done to make the organ’s actions as fast and articulate as possible.
All swell engines were rebuilt and their actions choked to achieve a seamless shade motion that was fast and silent. Any new wind lines, including all those from the blower room, are all soldered-galvanized metal. Numerous internal chamber wind lines were repaired and every flange gasket replaced. Reservoir wind box interiors were felted so that each acts as a sort of muffler, thereby keeping this giant wind system, of generous pressures, silent. Every screwhead was polished and for the best possible serviceability, all the chambers are washed with LED fluorescent lighting plus a generous sprinkling of service duplexes. The console is renewed inside and out. The organ has been totally rewired with new telecommunications cable as per NEC specs. The blower is totally rehabbed with a (necessary) new motor.
Perhaps because they’d been handled so seldom, the organ’s metal pipes cleaned up to a truly like-new appearance. Wood pipes also cleaned up beautifully; however, the very wide humidity swings common to Minneapolis saw the largest wood stops develop numerous cracks. Each of these were spline repaired. Although we’ve found this on a number of other organs, there were over a hundred pipes that had never been made to speak! It seems that overall pipe speech was, in places, hit or miss. This was a time when G. Donald Harrison and Ernest Skinner were speaking only when necessary and we wonder if either ever invested all the time necessary on tonal finishing; after all, whose job was it? We have utmost respect for this venerable Boston firm and its instruments, but just how this happened will be a question that looms forever. Needless to say, every pipe is now speaking beautifully.
The organ will be dedicated on October 12 and 13 with concerts by the Minnesota Orchestra (Osmo Vänskä, music director) with Paul Jacobs and a newly commissioned work for organ and orchestra by John Harbison. On December 4, Nathan Laube will perform the first solo organ recital. His masterclass follows the next day.
Besides our regular, 20-member, full-time staff, a few outside contractors assisted: David Beck played a significant part in assisting with shop and field flue voicing; Broome and Company reconditioned the reed stops; and OFS of South Windsor, Connecticut, refinished the console.
We much appreciated the input and help of university staff crucial to this project: Michael Denny (project executive), Roger Wegner (senior project manager), and Dean Billmeyer, university organist and professor of music.
As happens on some large projects such as this, we were subcontracted, in this case to the Northrop project general contractors, J.E. Dunn Corporation of Kansas City, Missouri. They, and all the above involved, were significant players and I’m happy to report that we enjoyed working with each and every person to finish this large organ project within budget and on time.
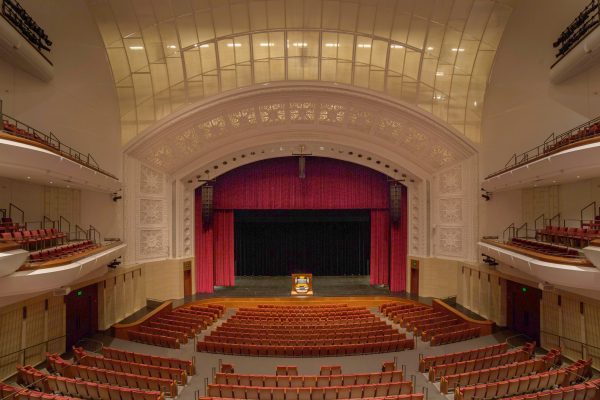
Mike Foley is president of Foley-Baker Inc.