150 Years of Schantz Organs
Schantz Organ Co.
By Luke Tegtmeier, Eric Gastier, Jeffrey Dexter, and Victor Schantz
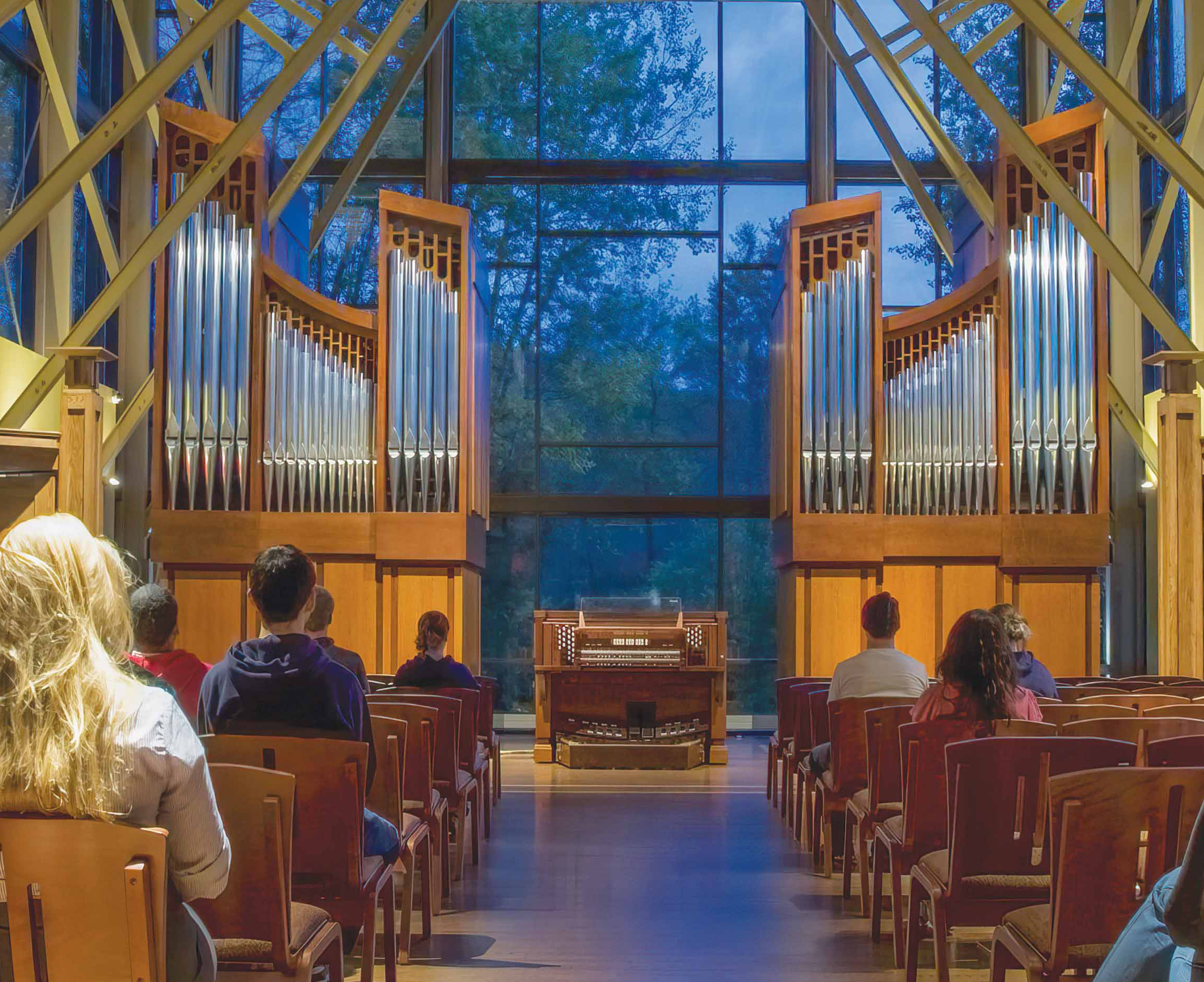
This year, the Schantz Organ Company is proud to celebrate the 150th anniversary of its founding by Abraham J. Tschantz.1 Today, the fourth and fifth generations of the family are leading the business, and over 3,000 Schantz instruments have been built in 46 American states and in Melbourne, Australia. This article will examine the history of the Schantz Organ Company, which was founded by a farmer’s son 150 years ago and has become one of the world’s largest and most venerable organbuilders.
The First Generation
The Tschantz family left Switzerland in 1824, searching for greater religious freedom after being persecuted for their Anabaptist (Mennonite) faith. They settled near Kidron, Ohio, where Abraham was born in 1849. A mechanically gifted young man, Abraham did not enjoy the family business of farming. To keep him on the farm, his father built the young man a workshop, where he began to build furniture. Around 1869 a reed organ in need of repair was brought to his shop. Even though Abraham had never worked with a musical instrument before,2 he was able to fix it. Two years later, he assisted the Votteler Organ Company of Cleveland, Ohio, with the installation of a new instrument at the Evangelical & Reformed Church in Winesburg, Ohio.3
These experiences inspired Abraham to start crafting his own musical instruments in 1873. He started small, building reed organs on the family farm. Family lore has it that he would often go to his workshop on Sunday mornings to play his instruments, causing passing Mennonites to slow down to listen on their way to worship. His business was successful enough that, only two years later, he moved to a new state-of-the-art shop with a steam-driven line-shaft system near the railroad in the neighboring town of Orrville, Ohio.4
Abraham’s reed organs were built under the trade name Ohio Beauty and were shipped all over the world. One was featured in an episode of the 1970s television series Little House on the Prairie.5
Shop records indicate that the first Schantz pipe organ was a mechanical-action instrument of two manuals and 21 ranks, built in 1891 for First United Brethren Church in Canton, Ohio. This instrument had an unusual facade, with a pair of wooden pipes amid the typical painted metal ones.6
The company grew quickly. In 1890, Abraham began building organ blowers, and in 1914 he secured a patent for an electric blower.7 The Zephyr Electric Organ Blower Company is a subsidiary of Schantz, and it now sells blowers to organbuilders throughout North America. In 1901, Abraham built a new factory four blocks south. This building has been listed in the National Register of Historic Places and is part of the shop to this day.
From 1891 until at least 1908, Schantz built dozens of mechanical-action (tracker) organs. At least one of these is still in use today: a II/15 instrument from 1904 at Second UCC in Tiffin, Ohio. In 1905, Schantz started to build organs with a tubular-pneumatic mechanism; this continued until at least 1926. The company continues to maintain several of these historic instruments.
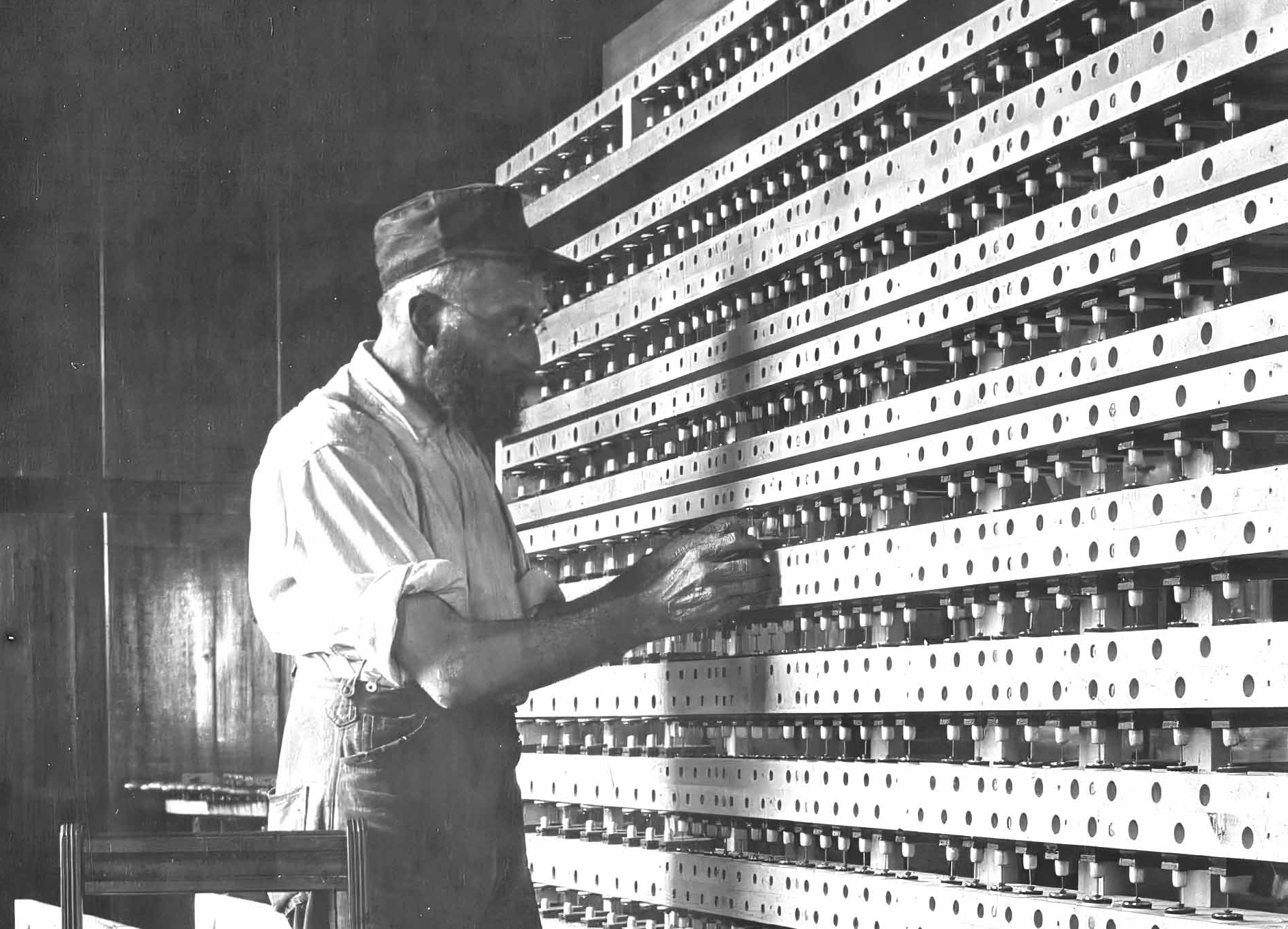
The Second Generation
Abraham and his wife, Katherine Gerber, had six children. All three of the boys took on leadership roles in the organ company when Abraham stepped down in 1913. Edison (1878–1974) worked on both tonal and visual design. Oliver (1882–1938) looked after sales and marketing. Victor A. (1885–1973) concentrated on technical aspects and shop management. He also spent 18 months as an apprentice at the Wurlitzer organ factory. According to shop legend, this is where he learned about electropneumatic action for pipe organs, and he brought this knowledge back to the Orrville factory.
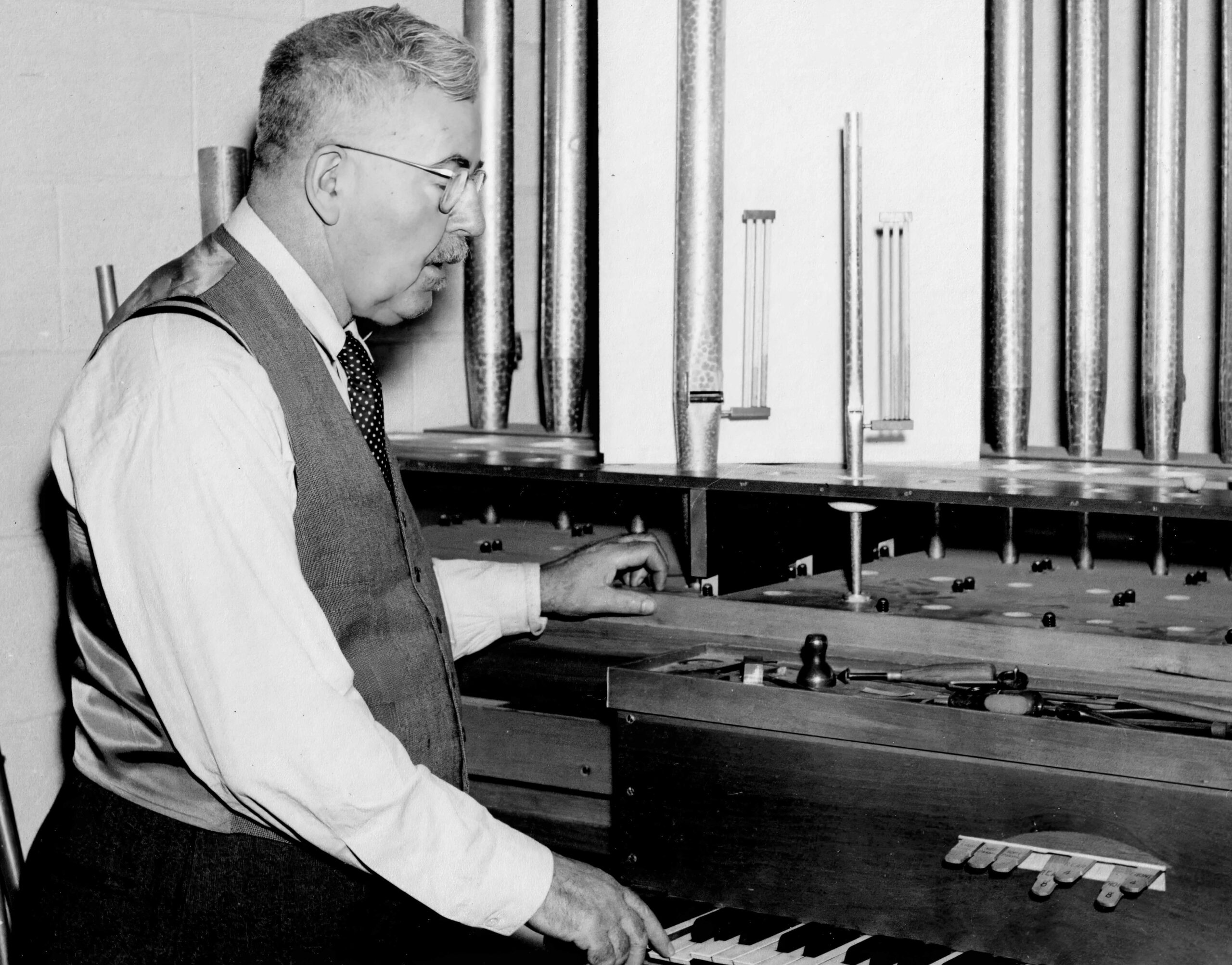
Perhaps because the shop was relatively small at the time, World War I does not seem to have had a major impact on the company. From 1914 until the outbreak of World War II, Schantz built more than 200 instruments, ranging from a 63-rank organ for St. Mary’s Catholic Church in nearby Massillon, Ohio, to a nine-rank organ for a church in Chicago. All but seven of the instruments from this period were installed in Ohio or surrounding states. At the outset of World War II, however, factories across the country were placed under government control. This included Schantz, which was assigned the task of constructing ammunition chests.8
The Third Generation
After World War II, churches around the country grew quickly, and Schantz expanded into a truly national company under the leadership of the third generation. Paul Schantz (1911–1997), the son of Oliver, had managed the shop throughout the war. After it ended, he continued in sales and marketing, establishing relationships with sales representatives from New Jersey to California. Alfred Lunsford (1922–2008), who was based in Knoxville, Tennessee, and Arthur Strahle (1909–1999), who was based in Flint, Michigan, were two especially important sales representatives.

Bruce Schantz (1913–2007), the son of Victor A., studied physics at Oberlin College, then worked at Goodyear Aerospace during World War II, building Corsair airplanes. After the war, he served as the shop foreman. Among his many accomplishments, he created the engineering department and trained three engineers: Chester Gable, Wilbur Herr, and Bob Romey. These men designed the layouts of organ chambers for more than 40 years.
John Schantz (1920–2013), also a son of Victor A., was drafted into the army during the war and served in the Philippines. A graduate of the Oberlin Conservatory, where he studied with the famed organist and pedagogue Arthur Poister, John took on the role of tonal director after the war. He was also a talented jazz pianist, and he especially enjoyed playing sessions with famous jazz musicians who were traveling between New York and Chicago.
In 1947, Jack Cook was hired. Jack was an Englishman who had spent most of his career working as a pipemaker at Skinner and Aeolian-Skinner. He used this talent to help design the Schantz pipe shop that was built in 1966. This new shop provided more space for casting metal and building pipes; it is still in use today.
Schantz stoplists from after World War II reflected the Orgelbewegung (Organ Reform Movement), moving from a majority of unison-pitch ranks to a greater emphasis on upperwork. Visual design changed as well. Facades featuring stenciled pipes became more rare, while simple chamber installations behind grille cloth became more common. Exposed “flower box” chests emphasizing the natural geometry of organ pipes were also built more frequently. During this period, the company experimented with new technology, such as building a proprietary combination action. The rapid expansion of churches after the war kept Schantz busy with new instruments, including its 154-rank magnum opus at the Cathedral Basilica of the Sacred Heart in Newark, New Jersey, which was built in 1953.
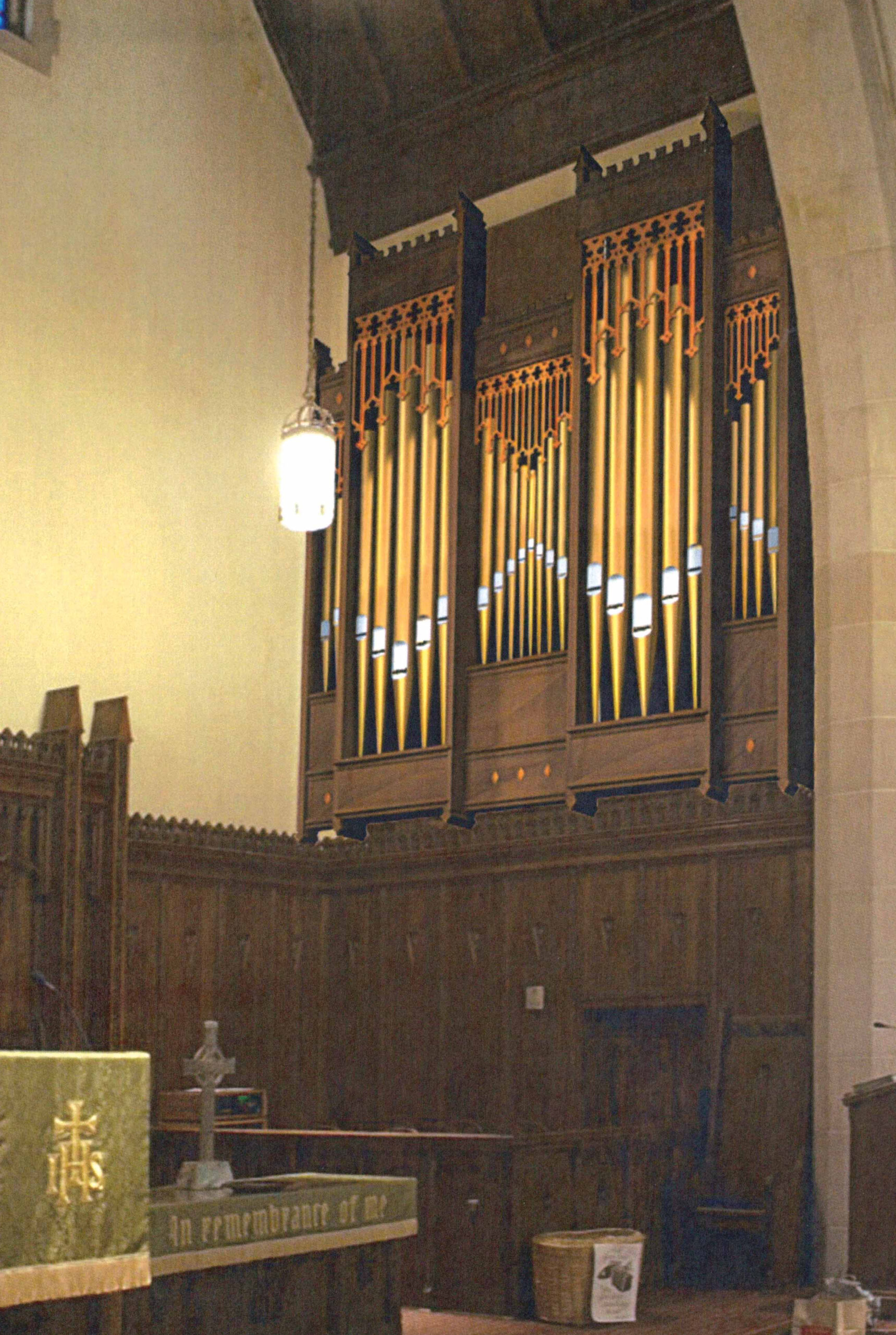
The Fourth Generation
Victor B. Schantz (b. 1953), son of Bruce, joined the company in 1973 and is president today. He has also been active in the larger community of organbuilders, serving two terms as president of APOBA (Associated Pipe Organ Builders of America) and serving on the boards of the AIO (American Institute of Organbuilders) and the new AOA (American Organ Academy). Victor was instrumental in leading Schantz through the details of working overseas for the Melbourne, Australia, project.9
In the early 1970s, concerns about Paul Schantz’s health led to the search for a company leader from outside the family. Jack Sievert (b. 1930) worked in sales and marketing from 1973 to 2008, helping to continue the growth of the company. Jack was a charming gentleman who was consulted by organists, committees, and organ technicians from around the country. He was also a charter member of the AIO.
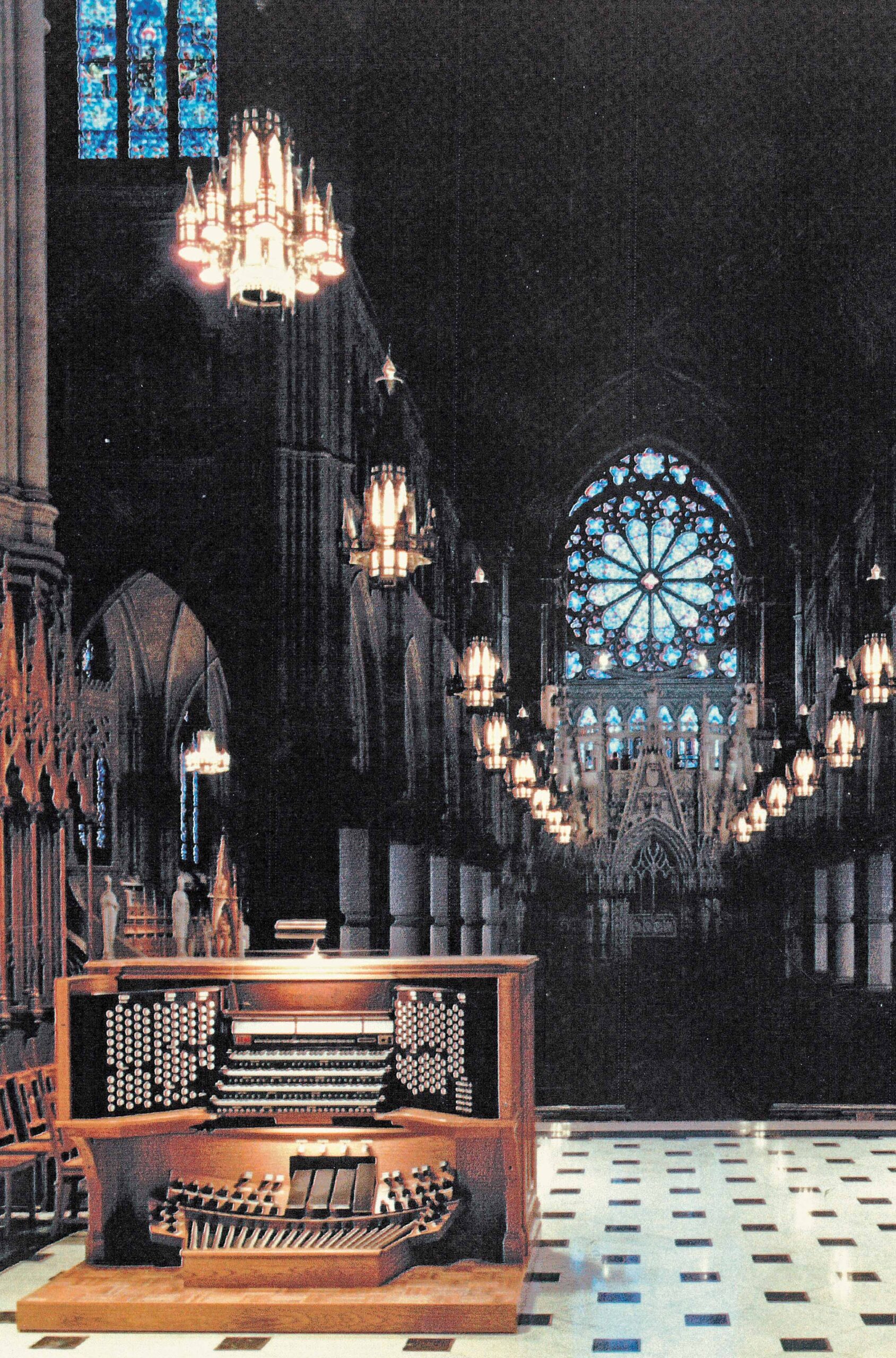
Following John Schantz’s retirement, Burton K. Tidwell (b. 1951) was hired as tonal director. Tidwell moved Schantz beyond the Organ Reform Movement constraints of the previous two decades. He also increased the attention given to on-site tonal finishing and developed an ingenious unit organ concept for clients with limited space and budgets.
By 1990, the shop was crowded with nearly 100 workers. Eric Gastier (b. 1964) and Jeffrey Dexter (b. 1962) were part of this growth. Eric’s primary role is staff architect. He works closely with clients, architects, and engineers to design casework and lay out organs. Jeffrey is tonal director; under his leadership, Schantz instruments continue to subtly shift toward broader scales and more singing tone, playing a wide range of repertoire effectively.
In 1993, Schantz undertook the first new chest-action development in a generation by building a Blackinton-style slider-and-pallet windchest for Painesville United Methodist Church in Painesville, Ohio.10 The company still builds this style of chest for the subtle tonal and spatial benefits it offers. In 1995, Schantz installed a CNC (computer numeric controlled) router to efficiently produce casework, pipe shades, console carvings, and mechanical parts. The router is also used to produce wood and metal parts for the pipe shop.
As the U.S. organ market shifted from a focus on new instruments to rebuilt and restored ones, Schantz craftsmen expanded their skills to restore organs from many other major North American builders. These include the 1927 Skinner (Opus 634) at the University of Chicago’s Rockefeller Chapel and the 1950 Möller (IV/79) at Central Presbyterian Church in New York City, which is currently in the shop.11
Today and the Future
Today, executive management consists of Victor B. Schantz, president, and Eric Gastier and Jeffrey Dexter, vice presidents. A fifth-generation Schantz family member, John P. (b. 1986), serves as comptroller. Luke Tegtmeier (b. 1983) joined Schantz in 2019 and serves as sales associate and service manager.
Recently completed work includes the restoration of the 1963 Aeolian-Skinner at the Metropolitan Opera in New York City,12 the rebuilding of Skinner and Kimball organs in Oklahoma, and the relocation of a Schantz from North Carolina to Cleveland, Ohio. The company is fortunate to have several major projects in its backlog, including new organs in Atlanta, New York City, and Sarasota, Florida, as well as major rebuild projects in Wisconsin, Pennsylvania, and New York City. Schantz also services nearly 200 instruments throughout Ohio and the surrounding states.
As part of its 150th-anniversary celebrations, Schantz hosted an open house on April 29, 2023, with more than 2,000 people walking through the shop to see how organs are built. The anniversary has been celebrated in many other ways as well, ranging from participation in local parades and events at the Tschantz family log cabin in Kidron, Ohio, to regular Facebook posts featuring historic photographs.
The Schantz Organ Company wishes to thank the thousands of churches, synagogues, universities, and other institutions and individuals who have become valued clients. The company is also thankful to the hundreds of people who have had a role in building pipe organs for the past 150 years. The company legacy is due to their hard work.
NOTES
1. The name would be changed to Schantz in 1899 to ease pronunciation as the business expanded. Other branches of the family have maintained the original spelling.
2. The Anabaptist tradition prohibits musical instruments in worship.
3. The Schantz Organ Company still cares for this I/8 tracker instrument.
4. The other major company in Orrville, J.M. Smucker, was founded in 1897.
5. The instrument was featured in season 5, episode 17; however, the 1979 show did not use the actual sound of the reed organ. Readers may be interested to know that the actor playing the instrument was Ray Bolger, who is best known for his role as the Scarecrow in The Wizard of Oz (1939).
6. For a picture of this organ, see The Diapason, Mar. 2023, 22.
7. Abraham also stayed busy with other ideas: he held patents for a disk harrow, an iron pump for wells, a pump to be used in water tanks for threshing machines, and a pneumatic oil can to fill kerosene lamps without spilling the kerosene. This last patent from 1890 was eventually sold to another company for the princely sum of $5,000.
8. Interestingly, the Aeolian-Skinner factory built coffins during World War II.
9. The Melbourne instrument was the Cover Feature of the October 2001 TAO.
10. The Painesville instrument was the Cover Feature of the October 1994 TAO.
11. The Rockefeller Chapel instrument was the Cover Feature of the October 2008 TAO.
12. For more information on the Metropolitan Opera instrument, see the November 2022 issue of The Diapason.
Luke Tegtmeier is sales associate and service manager for the Schantz Organ Company. Eric Gastier is staff architect and vice president. Jeffrey Dexter is tonal director and vice president. Victor Schantz is president.
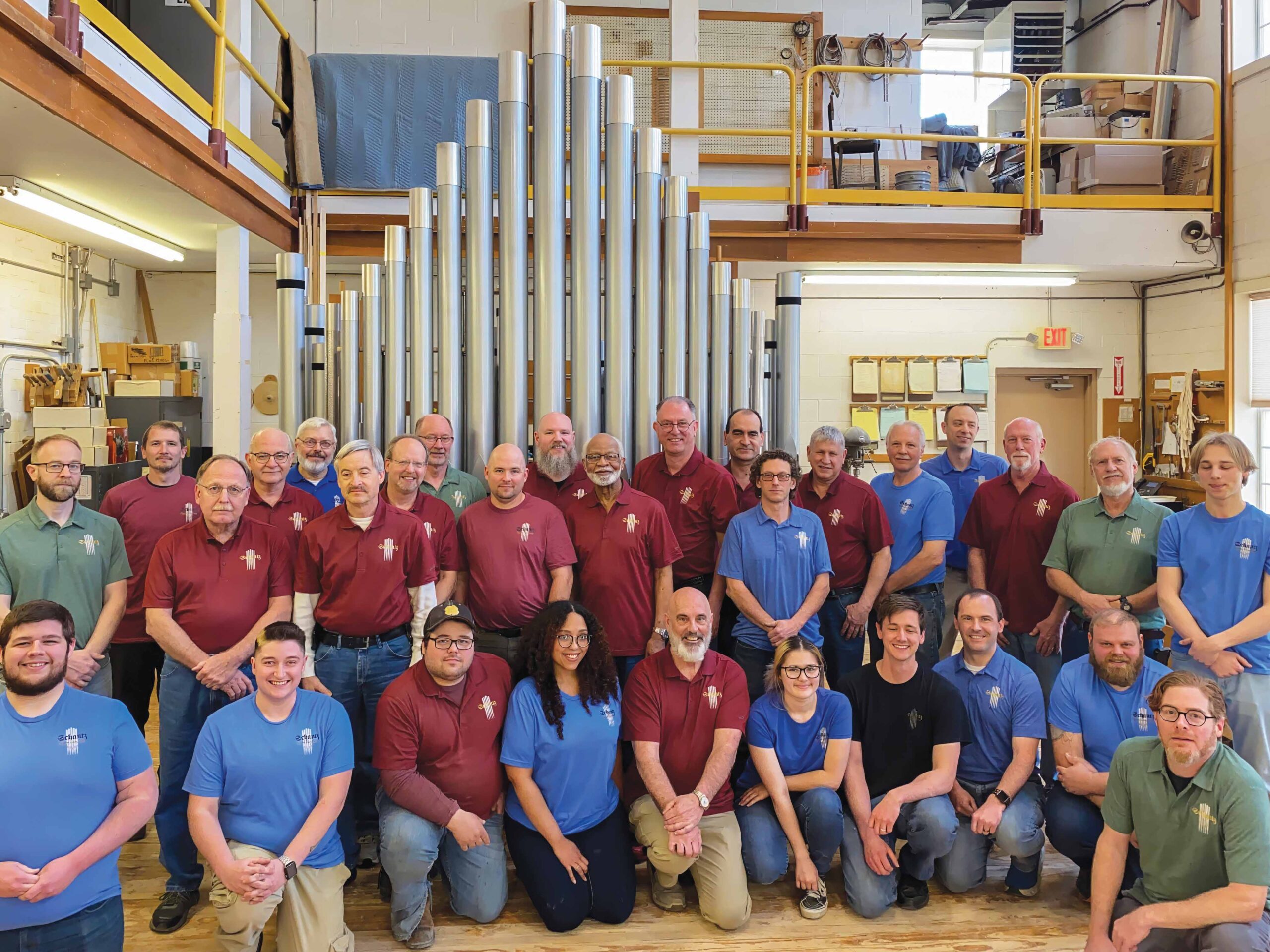
Schantz Organ Company Timeline
1824: Tschantz family emigrates from Switzerland to America and settles in Ohio
1849: Abraham Tschantz born
1873: Abraham starts building Ohio Beauty reed organs in a shop on the family farm near Kidron
1875: First factory built in Orrville
1891: First known pipe organ built for First United Brethren Church (Canton, Ohio)
1899: Family name changed to Schantz
1901: New factory built at the corner of East Oak and South Walnut Streets, still used today
1904: Oldest extant Schantz pipe organ built (II/15, Second United Church of Christ, Tiffin, Ohio)
1908: Last known tracker-action instrument built (II/9, First Methodist Church, Byesville, Ohio)
1913: Second generation takes on leadership
• Edison (1878–1974): visual and tonal design
• Oliver (1882–1938): sales
• Victor A. (1885–1973): foreman
1914: Zephyr blower patented
1926: Last known tubular-pneumatic-action instrument built (II/7, Trinity Episcopal Church, New Philadelphia, Ohio)
1946: Third generation takes on leadership
• Paul (son of Oliver, 1911–1997): sales
• Bruce (son of Victor A., 1913–2007): foreman
• John (son of Victor A., 1920–2013): tonal director
1947: Jack Cook hired from Aeolian-Skinner as pipe shop foreman; helps Schantz start making more pipes in-house
1953: Delivery of the Schantz magnum opus (IV/154) to the Cathedral Basilica of the Sacred Heart in Newark, New Jersey
1966: Pipe shop built for making new pipes
1973: Jack Sievert hired from Reuter as sales director (retired in 2008)
1985: Fourth generation takes on leadership
• Victor B. (son of Bruce, b. 1953): executive vice president (became president in 1998)
1988: Burton K. Tidwell hired as tonal director
1992: Eric Gastier hired as architect
1993: First Blackinton-style chest built (III/50, Painesville United Methodist Church, Painesville, Ohio)
1994: New three-story assembly room completed
1995: First CNC router installed for efficiently building wooden parts
1996: Jeffrey Dexter becomes tonal director
2000: First international project completed in Melbourne, Australia
2014: Fifth generation takes on leadership
• John P. (son of Victor B., b. 1986): comptroller